Training
What is Required from T8CCR 3314?
- Authorized Employees must be trained on hazardous energy control procedures and on the hazards related to performing activities required for cleaning, repairing, servicing, setting-up, adjusting, and unjamming prime movers, machinery, and equipment.
- Affected Employees must be instructed in the purpose and use of the energy control procedure.
- All Other Employees whose work operations may be in an area where energy control procedures may be utilized, must be instructed about the prohibition relating to attempts to restart or reenergize machines or equipment which are locked out or tagged out.
- The training must be documented as required by your Injury and Illness Prevention Program (T8CCR Section 3203).
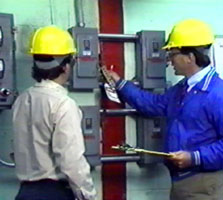
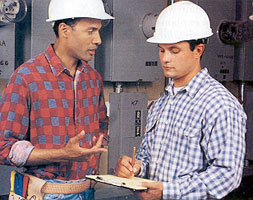
Best Practices - Training Your Employees
Employee training prior to work under lockout/tagout conditions or when using alternative measures is key. Lack of hazard awareness and knowledge in this area can result in death or serious physical harm. Therefore, all Authorized and Affected Employees (including other employees) must be trained. Remember that:
- Affected and Other Employees Do Not Perform Lockout or tagout (examples include maintenance and repair personnel, machine operators and janitors). These are employees whose jobs are either to:
- Clean, repair, service, set-up, adjust or unjamming machines and equipment under lockout or tagout, or
- Work in an area in which such activities are being performed under lockout or tagout.
- Affected and Other Employees must be trained on:
- The reasons for the Hazardous Energy Control Procedures and what they are used for
- The prohibition against restarting or reenergizing machines or equipment which are locked out or tagged out.
- The hazards of their work when performed under lock/out and tag/out conditions
- An Authorized Employee is a qualified person(s) who locks out or tags out specific machines or equipment so that cleaning, repairing, servicing, setting-up, adjusting or unjamming operations can be conducted. These employees must be trained:
- So they know the potential hazards of jobs and acquire the knowledge and skills necessary for the safe usage of the specific Hazardous Energy Control Procedures for each machine, piece of equipment or prime mover they are responsible for.
- The same individual may be both an Affected and Authorized Employee. If so, that person must receive the full range of training described above. For example, an individual may be responsible for performing lock/out or tag/out and operating, setting-up, repairing, cleaning, servicing, or adjusting the machine.
Once training is completed, document the names of the trainer and trainees with their signatures along with the date and subject of training.
How To Provide Training
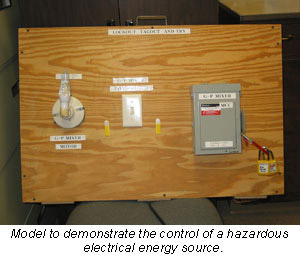
To be effective training must be provided in a language and at a level that employees understand.
Make your training specific to the actual work employees will be doing under lockout and tag/out. Effective training methods include:
- Small group discussion and exercises
- Practical demonstrations of ways of working safely under lockout or tagout
- Asking open ended questions to encourage employees to think about what they're doing as they work under lockout/tagout conditions. For example, you could ask: What types of hazards does your work activity have? What could be done to make working in your area safer?
To make sure your training is effective have employees talk to you about the newly learned material and demonstrate that they understand the information.
When Should Training Be Provided?
Employees must be trained before they are assigned to work under lockout and tagout conditions or before they use Alternative Measures. You should also train employees on lockout and tagout whenever:
- Near misses or accidents occur
- Your periodic inspects reveal that your Hazardous Energy Control Procedures are not up-to-date, effective, or being used properly.
- Whenever there are changes in your equipment or procedures where lockout or tag out applies