Hazardous Energy Control Procedures (HECPS)
What is Required from T8CCR 3314?
HECPS must be developed and documented in writing, and used for cleaning, repairing, servicing, setting-up or adjusting prime movers, machinery, and equipment.
- Each machine, piece of equipment or prime mover must have separate procedural steps for their safe lockout/tagout.
Exception
The same procedural steps may be used for the safe lockout / tagout of groups or types of prime movers, machines or equipment, under the following conditions:
- Operational controls are configured in a similar manner, and
- Locations of disconnect points (energy isolating devices) are identified, and
- The sequence of steps to safely lockout or tagout the machinery or equipment are similar.
OR
- Machinery or equipment has a single energy supply that is readily identified and isolated and has no stored or residual hazardous energy.
The HECPS must clearly and specifically outline at least the following:
- The machines, equipment, operations, and processes where they apply (i.e., scope)
- What the procedures are used for (i.e., purpose and intended use)
- The name of the people who will carry out the procedures (i.e., authorization)
- Rules for carrying out the procedures
- The means to enforce compliance with the procedures
- Techniques used for the control of hazardous energy
- The steps (meaning the procedures and requirements) for:
- Shutting down, isolating, blocking, and securing machines or equipment to control hazardous energy;
- The placement, removal, and transfer of lockout / tagout devices and who is responsible (i.e., responsibilities) and,
- Testing to determine and verify the effectiveness of lockout and tagout devices and other hazardous energy control devices.
Best Practices - How to Develop Your HECPs
Listed below are the general steps for writing your HECPs. This is followed by more information on each step to help you develop and put into place your HECPs.
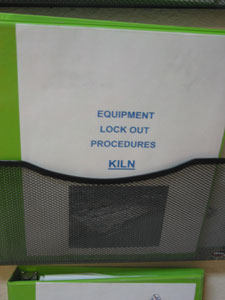
- Step 1 - State the purpose and use of your HECPs
- Step 2 - Name the Authorized Employee(s) responsible for carrying out the HECPs and restoring equipment, machines, and prime movers back to service
- Step 3 - Develop specific procedures for the transfer of responsibilities
- Step 4 - State the rules that apply to your HECPs and how you will enforce compliance
- Step 5 - List all the equipment, machinery, prime movers, and ALL their source(s) of hazardous energy that your HECPs apply to
- Step 6 - For each piece of equipment, machinery or prime mover describe the specific techniques and steps to follow in order to control all hazardous energy sources, and how to safely restore the machinery and equipment to service
- a. Consider work activities
- b. Specify hazardous energy control steps
- c. Secure hazardous energy control points
- d. Test for effectiveness
- e. Restore equipment, machines, and prime movers back to service
Remember that the specific procedures that you need to develop to protect workers depends on:
- Your machines, equipment and prime movers, and
- Their sources of hazardous energy, and
- The work activities being performed
MORE ON THE STEPS
Employee participation in developing your HECPs is extremely valuable because they can provide valuable information and help identify deficiencies. Also employee participation promotes their acceptance and compliance with the procedures.
Posting your HECPs on or close to the equipment/machine serves as a reminder and improves compliance.
Step 1 - State the purpose and use of your HECPs
Step 2 - Name the Authorized Employee(s) Responsible for Carrying Out the HECPs and Restoring Equipment, Machines, and Prime Movers Back to Service
- Remember, your HECPs can only be carried out by Authorized Employees
- Develop a way to notify all Affected Employees that a lockout is required and the reasons for it
Step 3 - Develop Specific Procedures for the Transfer of Responsibilities
- Procedures must be designed to ensure the orderly transfer of lockout or tagout device protection between off-going and incoming employees, to minimize exposure to hazards from the unexpected energization or start-up of the machines, equipment or prime movers.
- Develop procedures in advance for the transfer of responsibility when the Authorized Employee(s) who applied the lockout or tagout device(s) is not available to remove them (such as during shift or personnel changes). Steps should include:
- Informing all Affected Employees
- Confirming that the Authorized Employee who applied the device(s) is not at the facility
- Making all reasonable efforts to contact the Authorized Employee who applied the device(s) and inform them that the device(s) have been removed
- Naming in advance the new Authorized Person(s) responsible for the removal of the device(s)
- Specifying the specific steps necessary for the new Authorized Person (s) to remove the lockout or tagout devices that were originally placed (e.g., transfer of keys for locks, or transfer of tags or signs or placement of new locks or tags and signs, etc.)
Step 4 - State the rules that apply to your HECPs and how you will enforce compliance
Step 5 - List All the Equipment, Machinery, Prime Movers, and ALL their Source(s) of Hazardous Energy that your HECPs apply to.
For each of your machines, equipment, or prime movers make sure to identify all their sources of hazardous energy, and the magnitude of each energy source. Remember that each machine, piece of equipment, or prime mover may have multiple sources of hazardous energy feeding into them. Examples of types of hazardous energy sources include: electrical, mechanical, hydraulic, pneumatic, chemical, thermal, potential, stored, and others.
Once identified, label all hazardous energy source(s) for all machines and equipment to prevent employees from mistaking the machines or equipment it feeds.
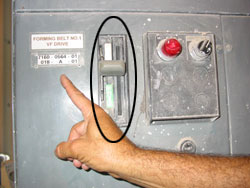
Labeled electrical energy isolation device
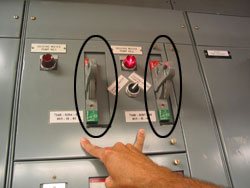
Electrical energy sources with 2 labeled energy isolating devices (switches)
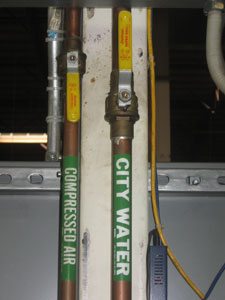
Labeled pneumatic and hydraulic energy sources
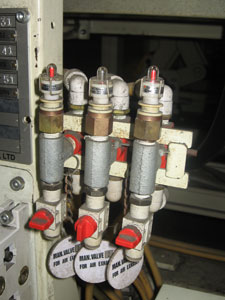
Pneumatic hazardous energy sources labeled
Label identifies flexible conduit delivering electrical energy to motor
Step 6 - For each piece of equipment, machinery, or prime mover describe the specific techniques and steps to follow in order to control all hazardous energy sources and how to safely restore the machinery and equipment to service
a. Consider Work Activities
First consider the work activities of each Authorized or Affected Employee on the specific machine or piece of equipment, and the potential for injury from hazardous energy sources. Your HECPs must contain procedures to notify all Authorized and Affected Employees each time before any work activities involving lockout / tagout start.
b. Specify Hazardous Energy Control Steps
Then specify the steps to control all hazardous energy sources for each machine, piece of equipment or prime mover that you identified. In your procedures, remember to identify and control all hazardous energy sources including main and secondary power supplies, potential, and stored energy (e.g., capacitors, springs, elevated machine members, rotating flywheels, hydraulic systems, and air, gas, steam or water pressure.)
There are three basic ways to control hazardous energy sources which are isolation, blockage, or dissipation at points of control. Include steps and procedures for:
- Shutting down operating equipment by the normal procedure (e.g., depressing a button, opening a toggle switch)
- Hazardous energy control such as:
- Closing switches, valves
- Bleeding or draining valves
- Inserting blank flanges
- Dissipating, disconnecting, relieving, or restraining potential and stored energy by grounding, repositioning, blocking or bleeding. If there is a possibility of re-accumulation of stored energy to hazardous levels, verification of isolation shall continue until the work is completed.
Using a tool to verify there is no air pressure in the line
Bleeding air pressure by opening a valve
c. Secure Hazardous Energy Control Points
You must now develop procedures to ensure that the control measures can not be overridden or by-passed. Hazardous energy sources are considered adequately secured for each machine, piece of equipment, or prime mover when an unplanned event would not reactivate the flow of energy or cause inadvertent movement.
Your procedures must specify how lockout and tagout devices will be placed and removed, and if necessary transferred between employees at the point of control. They must also specify who is responsible for each of these functions. There are two basic ways to secure hazardous energy points of control. These are:
- Lockout - using personal padlocks (where only the authorized person has the key) or seals that can be readily secured to the point of control
- Tagout - posting accident prevention signs and tags which can be readily secured to the point of control. Tagout device attachment means must be of a non-reusable type, attachable by hand, self-locking, and non-releasable with a minimum unlocking strength of no less than 50 pounds.
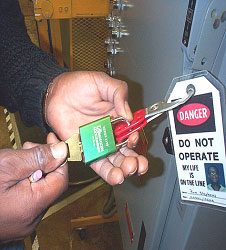
Electrical control panel locked out/tagged out
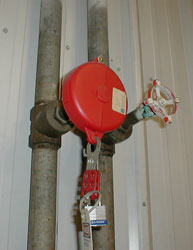
Hydraulic gate valve locked out/tagged out
Pneumatic valve locked out/tagged out
d. Test for Effectiveness
Once your hazardous energy control procedures have been developed you must also develop procedures to test their effectiveness. These procedures should specify that testing be done each time you de-energize your machines, equipment, and prime movers regardless of the time interval between de-energizing and start-up. Your procedures should also specify that where there is a possibility of re-accumulation of energy to hazardous levels, testing should be continued until work activities are completed. Procedures for testing should include:
- Removal of employees from the area of the machine, equipment, or prime mover
- Having Authorized Employee push the start button to activate the machine, equipment, or prime mover to make sure it does not start. This means all energy sources have been positively locked out
- Returning controls to the "off" position following testing which means the machine, equipment, or prime mover is now locked out.
If sensing devices are used for testing they must be used according to established procedures and be regularly inspected and/or calibrated.
e. Restore Equipment, Machines, and Prime Movers Back to Service
You must develop procedural steps for the removal of lockout and tagout devices. The same Authorized Employee(s) responsible for carrying out the Hazardous Energy Control Procedures should be responsible for restoring machines, equipment, and prime movers back to their normal operation. Steps include:
- Installing guards and verifying that the equipment is fully assembled and ready to resume safe operation.
- Removing unnecessary tools, spare parts, etc.
- Notifying all employees who would be affected by the startup of the equipment to be safely positioned before the lockout device(s) are removed.
- Removing materials and hardware (i.e., locks, tags etc.)
- Re-energizing machines, equipment, and prime movers
Remember, you must also develop in advance a procedure for the transfer of responsibility when the Authorized Employee(s) who applied the lockout or tagout device(s) is not available to remove them (see Step 2, above).