How Do You Control the Hazard? Hazards of Silica in Construction
Whether it's silica dust or anything else that employees are being overexposed to, you want to control the problem by starting at the top of the following sequence. Reference T8CCR, Section 5141 for details on how Cal/OSHA requires this hierarchy of controls. Go to Respirable Crystalline Silica Standards - Important Update for guidance.
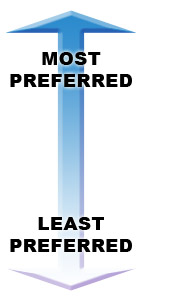
Eliminate or reduce the silica content.
"Engineer" out the exposure - i.e. use an effective local exhaust or vacuum tool system, wet-cutting and/or isolate the source of dust.
Use administrative and work practice controls, such as limiting the amount of time of exposure and working with materials in a way that reduces the generation of airborne dust.
Use personal protective equipment, such as a respirator and coveralls that keeps the dust off the clothes you wear home. Respirators may still be required if the above controls don't adequately reduce exposure levels.
Isolation
- Enclose the work so all dust is contained within the enclosure and all employees are outside.
- Establish a perimeter around the source of the airborne dust to keep employees away and prevent exposures.
In both cases, careful attention is needed where employees need to enter the affected area once the process has stopped or the enclosure has been removed. There may be considerable dust contamination that can easily become airborne due to traffic and other activities, such as clean up.
Ventilation
Use a local exhaust or vacuum tool system that removes airborne dust before it gets to the breathing zone of the operator or surrounding employees.
Some important things to watch out for:
- The exhaust system needs to be properly designed in order for it to effectively control exposure. This means an exhaust hood design that allows for effective capture of airborne dust.
- The users need to make sure it is consistently set up according to the manufacturer's specifications, and remains so throughout its use. This includes using the shortest flexible ducting with the least amount of bends.
- The system needs to be maintained to ensure optimal air exhaust. This includes ensuring the dust collectors are serviced as needed. NOTE: Maintenance of the system can result in significant dust exposures, so respiratory protection may be needed.
- User training on the proper use and maintenance of the equipment.
Wet-Cutting
Use a wet-cutting system that minimizes the generation of dry dust.
What to watch out for:
- Systems meeting Nationally Recognized Testing Lab (NRTL) approval requirements for electrical systems in wet conditions, including GFCI-protected electrical sources.
- Set up and maintenance of the equipment according to the manufacturer's instructions. This will include ensuring water flow rates within specifications.
- User training on the proper use and maintenance of the equipment.
Work Practice Controls
DO's
- Work with materials in a way that minimizes the generation of airborne dust.
- Wet sweeping where possible using water or a sweeping compound.
- Use vacuums and exhaust systems with adequate filtration. Reference Section 1532.3
- Wet materials before disturbing, unless that creates significant muscular skeletal strain, slip or other safety hazards.
- Use a water mist to keep airborne dust down.
DON'Ts
- Work with materials dry unless you also have a good exhaust system or there is simply no other way to do it safely, in which case a good respirator protection program will be necessary.
- Use compressed air to clean dust off of surfaces, equipment or yourself.
Respirator Protection
If your employees are using one, then make sure that they are doing so via a respirator protection program that meets Section 5144 requirements, including:
- They are using the right one for the type of material in question. This means
- The filter will filter out the particle size employees are being exposed to, as well as any other hazardous materials, such as solvents, that may be present.
- The respirator's protection factor is suitable for the exposures being encountered.
- They are medically approved to wear one.
- It fits them properly. This means the user needs to
- Do a positive/negative fit check every time they put a respirator on.
- Undergo a qualitative or quantitative fit-test at least annually.
- They've been trained on the respirators' limitations and how to properly use, clean and store it.
- This includes making sure they do not have facial hair that breaks or interferes with the seal between the respirator and their face.
- Someone in the organization has been given the responsibility to make sure the program is being implemented correctly.
Other Sources of Information
Cal/OSHA
Respirator Protection: Guidelines on how to make sure you as the employer have an effective respirator protection program that includes:
- Selection of the appropriate type.
- Medical approval.
- Fit-testing.
- Training on how to wear and maintain.
NIOSH
WISHA
OSHA
OSHA guidance document "OSHA's Respirable Crystalline Silica Standard for Construction". Note that this guide references the OSHA program and related standards. Employers in California need to abide by Cal/OSHA regulations.
June 2019